Manufacturing
The impact of digital industrial transformation on organizations, their suppliers, consumers, and other third parties is enormous. Whether you're selling precision machinery or building materials online, technology can benefit you in various ways. Digital technologies assist manufacturers in improving operating efficiencies and optimizing several business sectors, ranging from product creation to supply chain management.
Advanced manufacturing technologies have several benefits, such as assisting organizations in unlocking digital business models, adapting to changes faster, and even anticipating changes before they occur - all of which are critical to manufacturing. So it's hardly surprising that IDC predicts that by the end of 2022, half of all manufacturers will have invested in smart manufacturing through increased resilience, data analytics, and artificial intelligence.
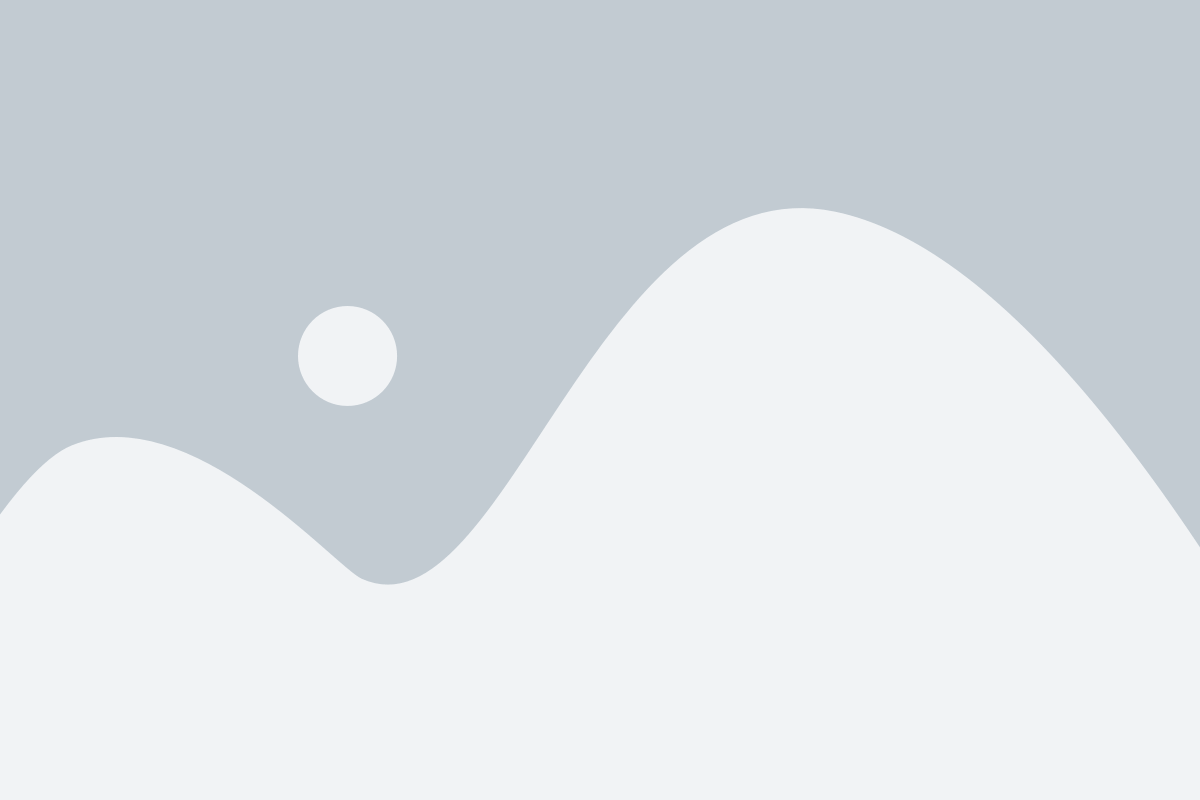
Industry 4.0
The term "Industry 4.0" refers to the integration of traditional manufacturing, industrial plants, and smart technologies throughout value and supply networks. The major goal of Industry 4.0, often known as "the fourth industrial revolution," is to automate manufacturing processes to the point where all activities are automated and controlled digitally in real time.
A fourth industrial revolution technology might be a machine with integrated sensors that interact with another machine depending on sensors' data, all without another human's intervention. In the future, Industry 4.0 may erase the distinction between physical and virtual warehouses, allowing employees to collaborate more effectively.
E-Commerce
Selling to businesses is challenging, and using a platform that does not meet the needs of today's corporate buyers can be counterproductive. For example, Wastequip, a major manufacturer of waste management equipment, began its digital transformation with the strategic goal of simplifying client orders. The company used a B2B eCommerce solution to establish an easy-to-navigate site where clients could search, order, and monitor their transactions. Wastequip's digitalization through eCommerce has been a success: it has allowed the company to expand its online presence, with an 8x increase in web traffic.
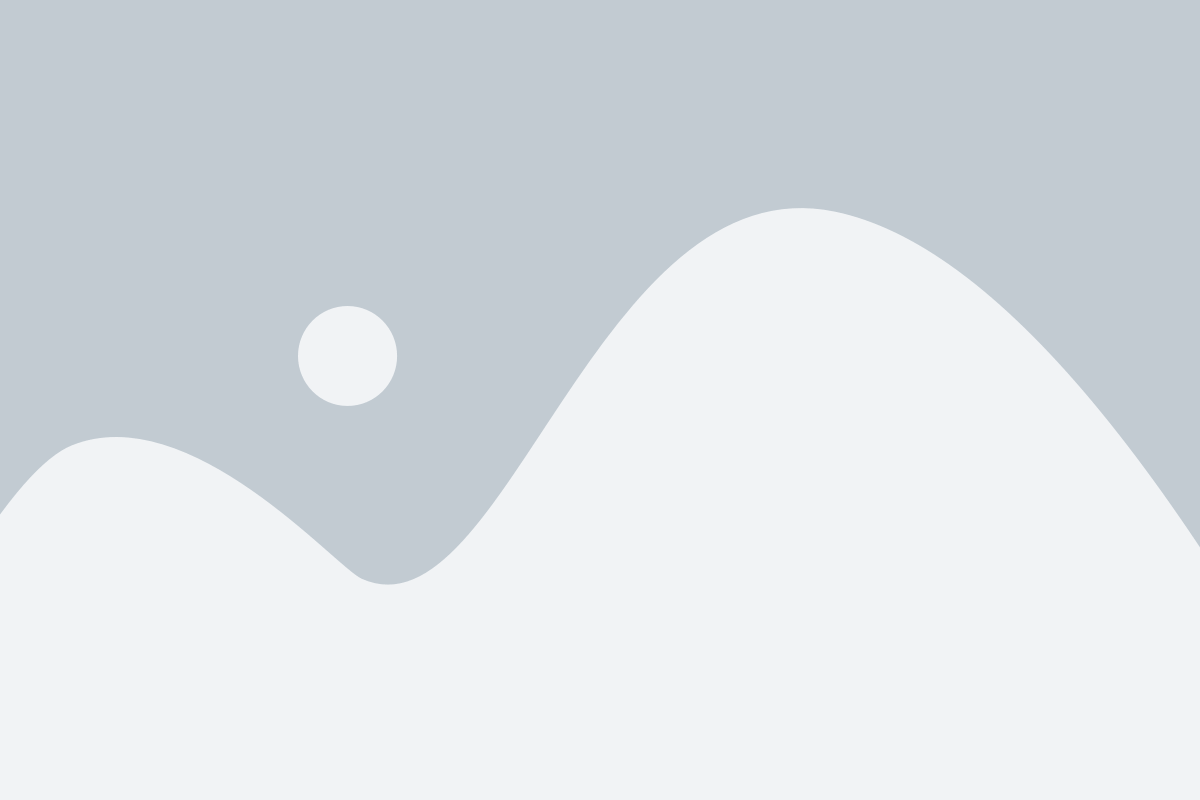
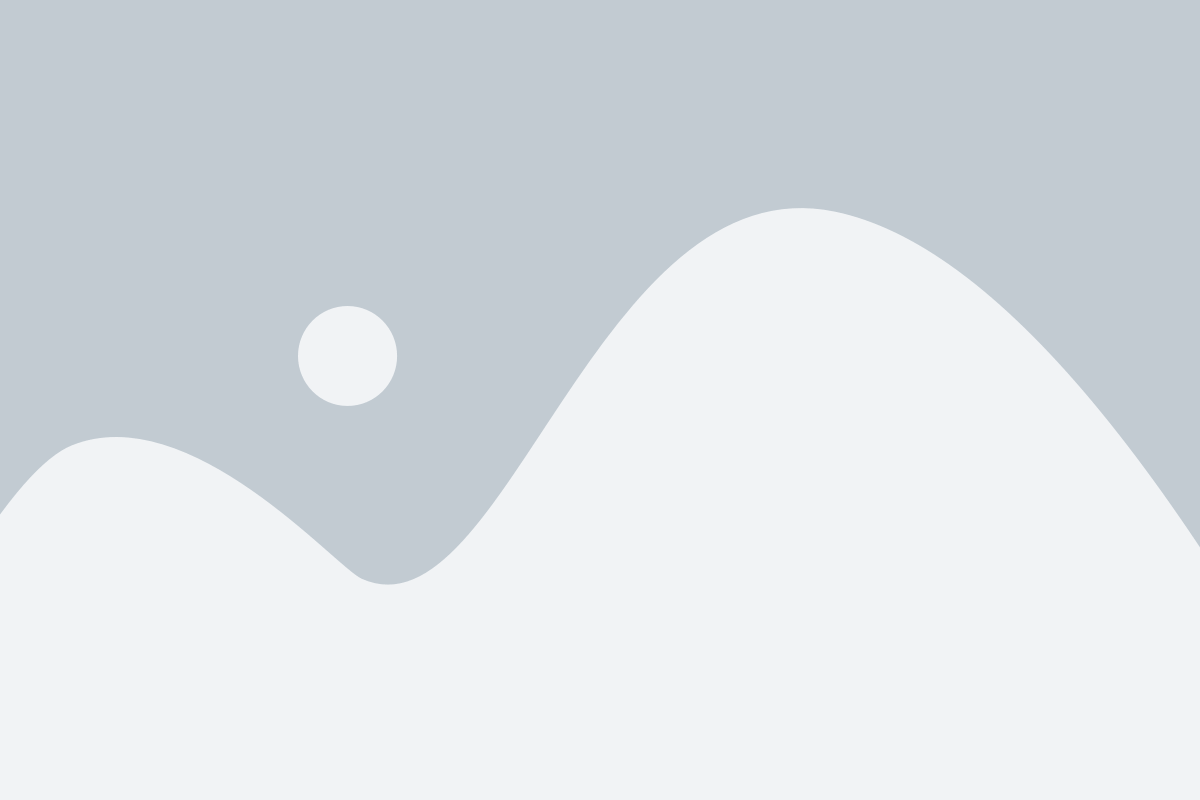
Big Data and Data Analytics
The importance of big data in manufacturing cannot be overstated: NIST demonstrated that with machine learning alone, General Electric enhanced production capacity by up to 20% while reducing material consumption rates by 4%.
Without employing a single employee, one California-based fruit provider raised productivity by 50%. What made the difference was a data-driven historical analysis, alarm notification, and other big data reporting features built into the automation system.
IOT
The Internet of Things (IoT) is a major technology of Industry 4.0. It is a network of interconnected physical things that communicate depending on computed data and their environment, including data fed from outside. Embracing IoT can provide manufacturers with new functionalities, insights, services, and benefits.
Operations, asset management, and personnel management are the most prevalent IoT application cases. Manufacturers, for example, can use IoT to build preventative maintenance programs with real-time monitoring and improve energy efficiency and working conditions through intelligent air management, risk management, worker productivity, and more.
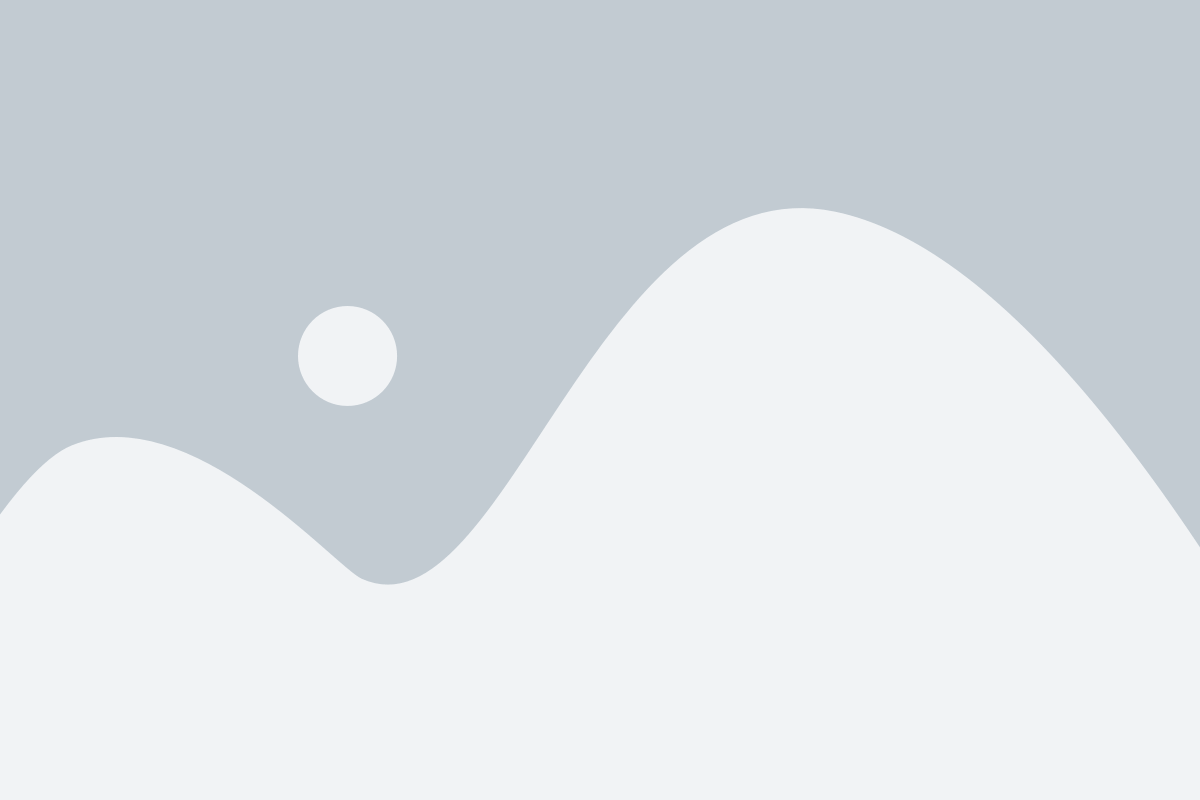
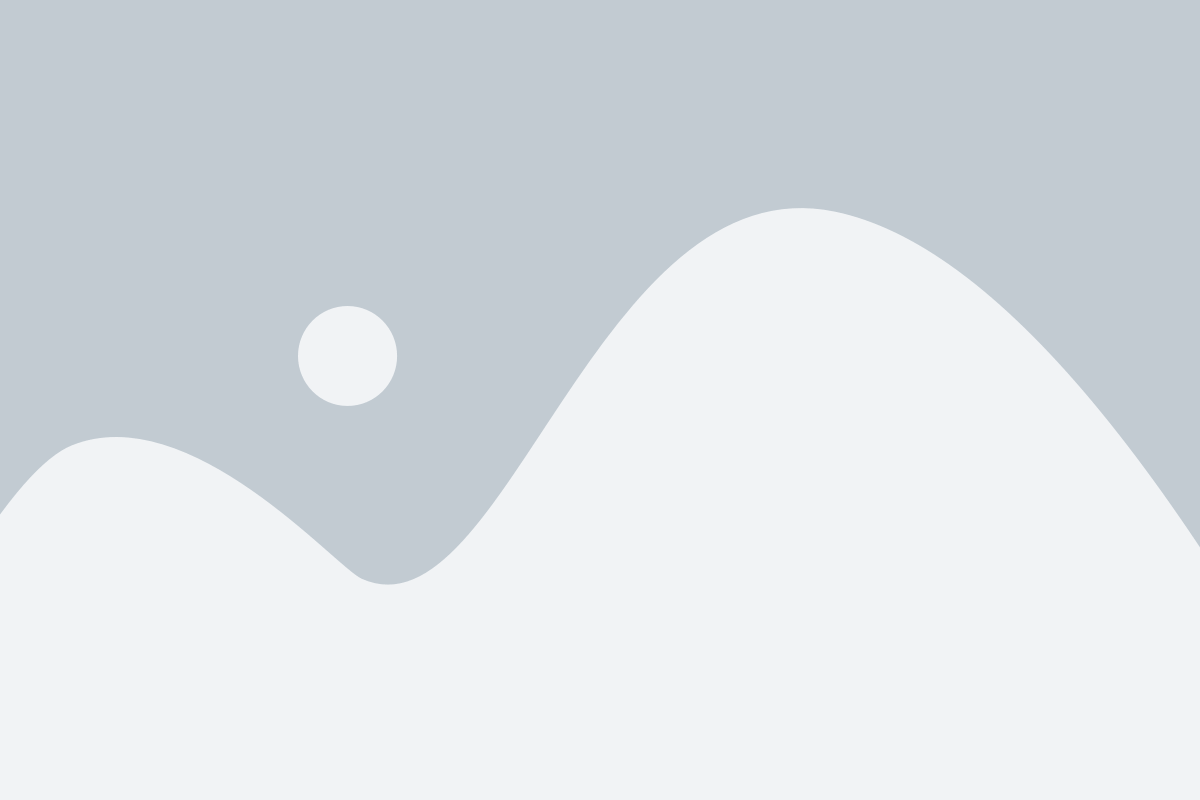
Machine Learning
With the quantity of data that machines are collecting, it is easier than ever to use algorithms to quickly perform the optimal course of action among various possibilities - something that humans would be far too slow to do. Today's machines have demonstrated that efficiency does not imply sacrificing quality, as machines can more precisely identify and forecast which aspects will affect production or assembly line speed and quality.
Machine learning can be used to advise the best course of action for employees, estimate waiting times and delivery delays, or create behavior models for supply chain risk avoidance. Another example is the use of artificial intelligence (AI) in eCommerce. When machine data is linked across the supply chain, it provides insights into all aspects of the manufacturing process.
Robots
Future robots are unlikely to differ significantly from what we see in industry now. What will change is the ability to learn from previous behavior and the use of pattern recognition to improve results. The number of linked devices, their interactions with one another, and the volume of data are all predicted to grow.
New robotics technologies will continue to evolve against the backdrop of connectivity, particularly in autonomous driving, dexterous carrying, moving, and so on. As robots become more independent, versatile, and cooperative, they can do increasingly complicated jobs, freeing employees of repetitive duties and enhancing manufacturing floor efficiency.
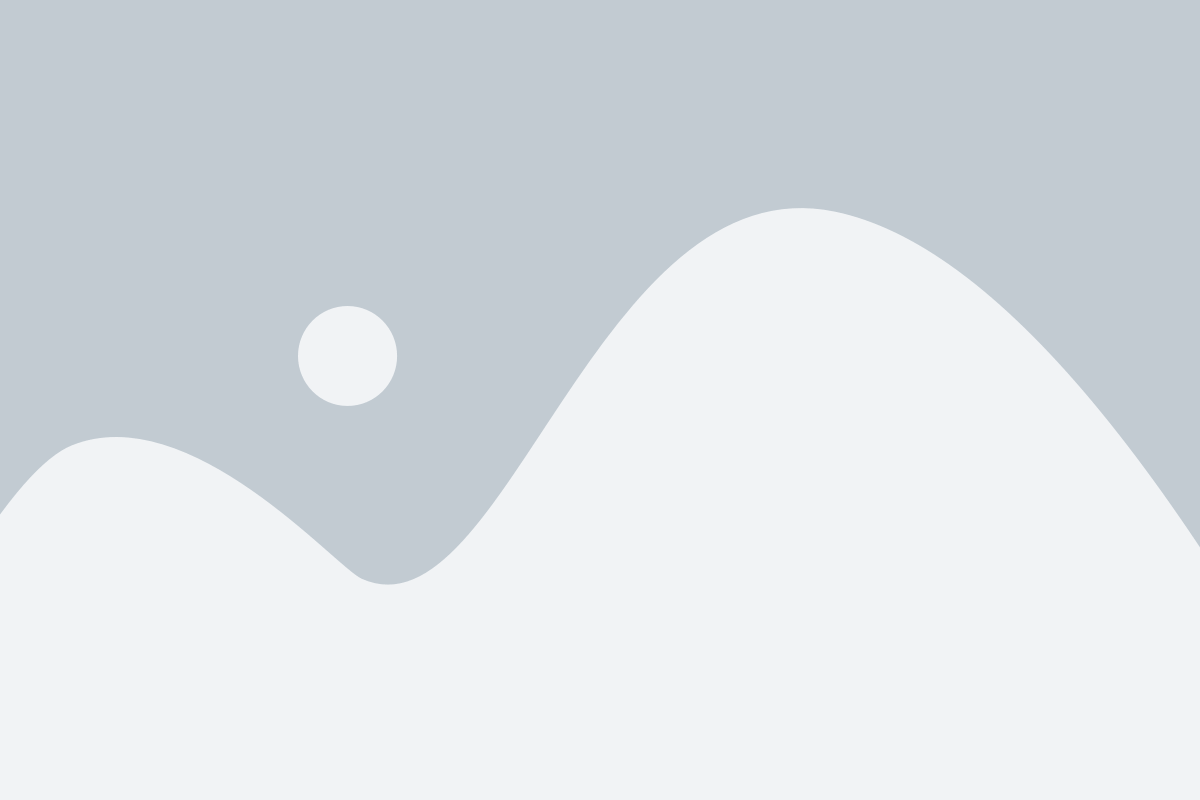
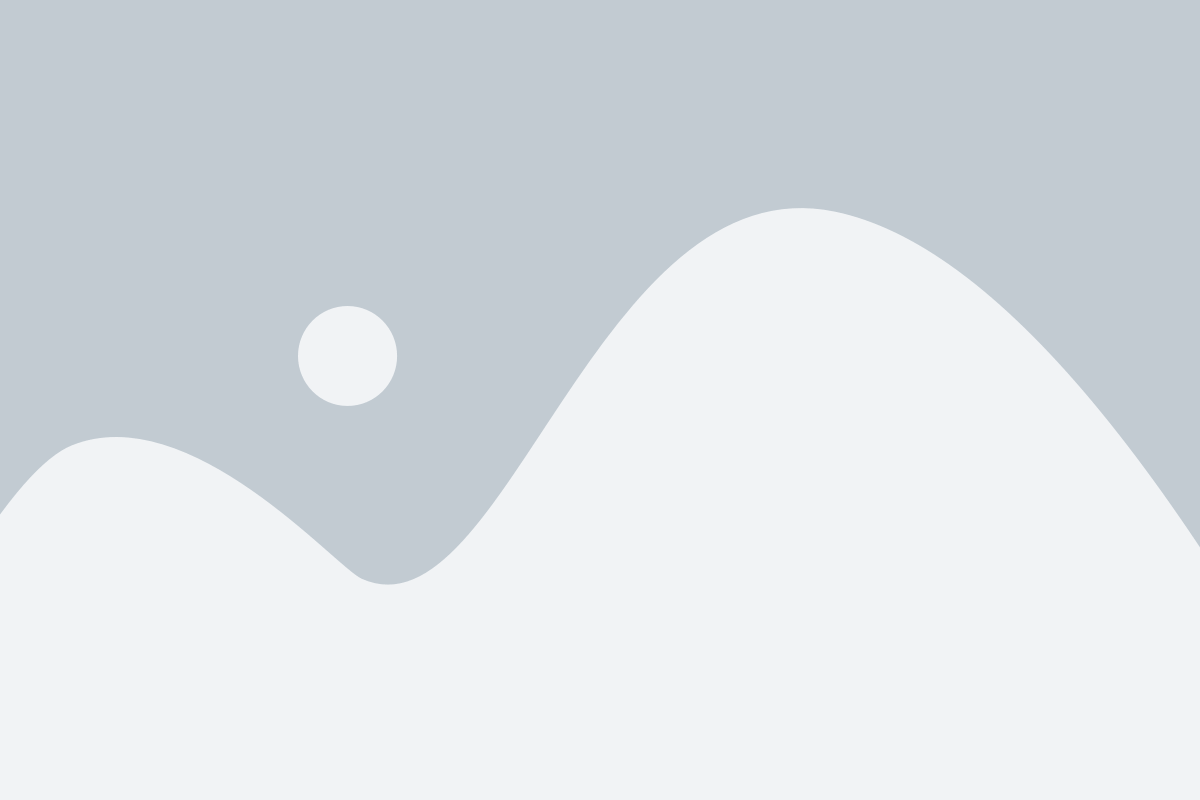
Additive Manufacturing
Along with robots and intelligent systems, additive manufacturing, or 3D printing, is a major technology that provides prospects for digital transformation. Additive manufacturing is a technology that uses digital 3D models to manufacture things layer by layer with a 3D printer. 3D printing is frequently a more cost-effective manufacturing choice than more traditional technologies for complex, detailed things.
Modern manufacturers include 3D printing into their digital strategy to reduce time-to-market for new goods, boost profitability, and support operational improvements.
Digital Twins
The concept of a digital twin has enormous potential for improving the performance and upkeep of production systems. A digital twin is a digital version of a physical product, machine, process, or system that enables businesses to better understand, analyze, and optimize their processes via real-time simulation.
An operator, for example, can utilize a digital twin to determine why a machine part is malfunctioning or to anticipate the lifetime of a product. This continuous, real-time simulation aids in the improvement of product designs as well as the uptime of equipment.
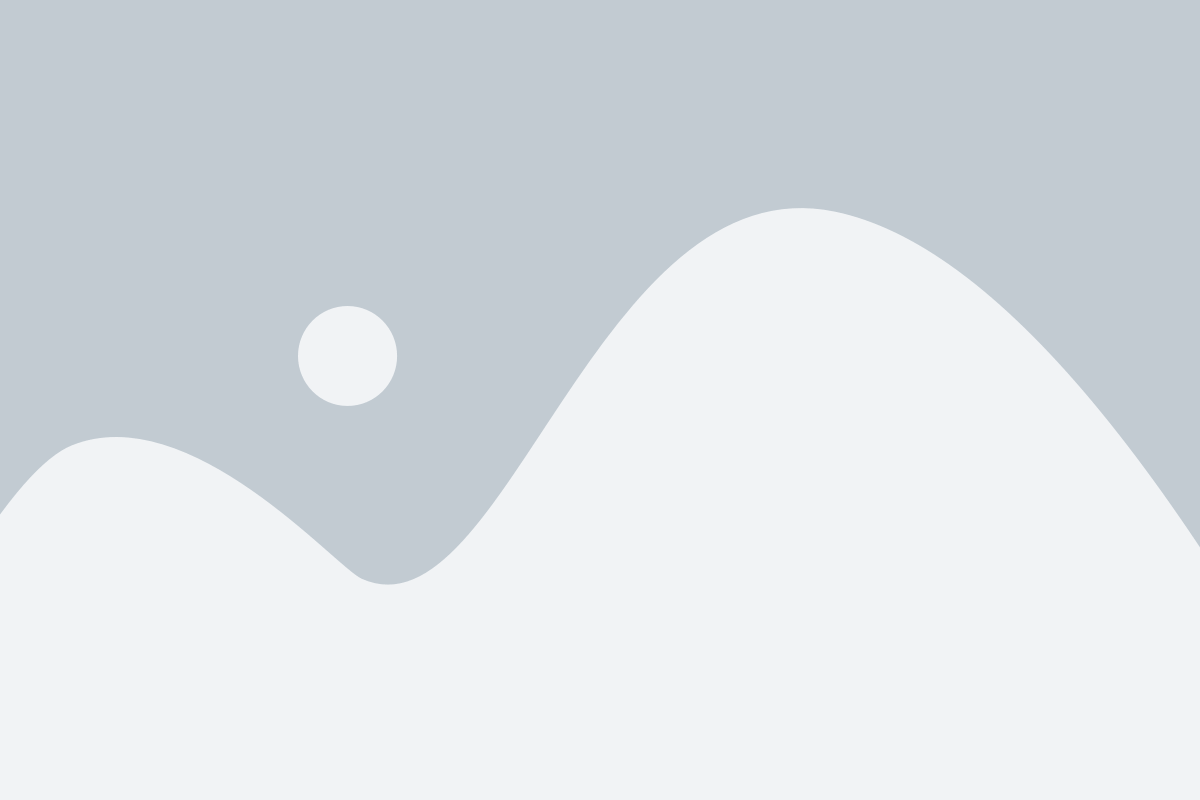
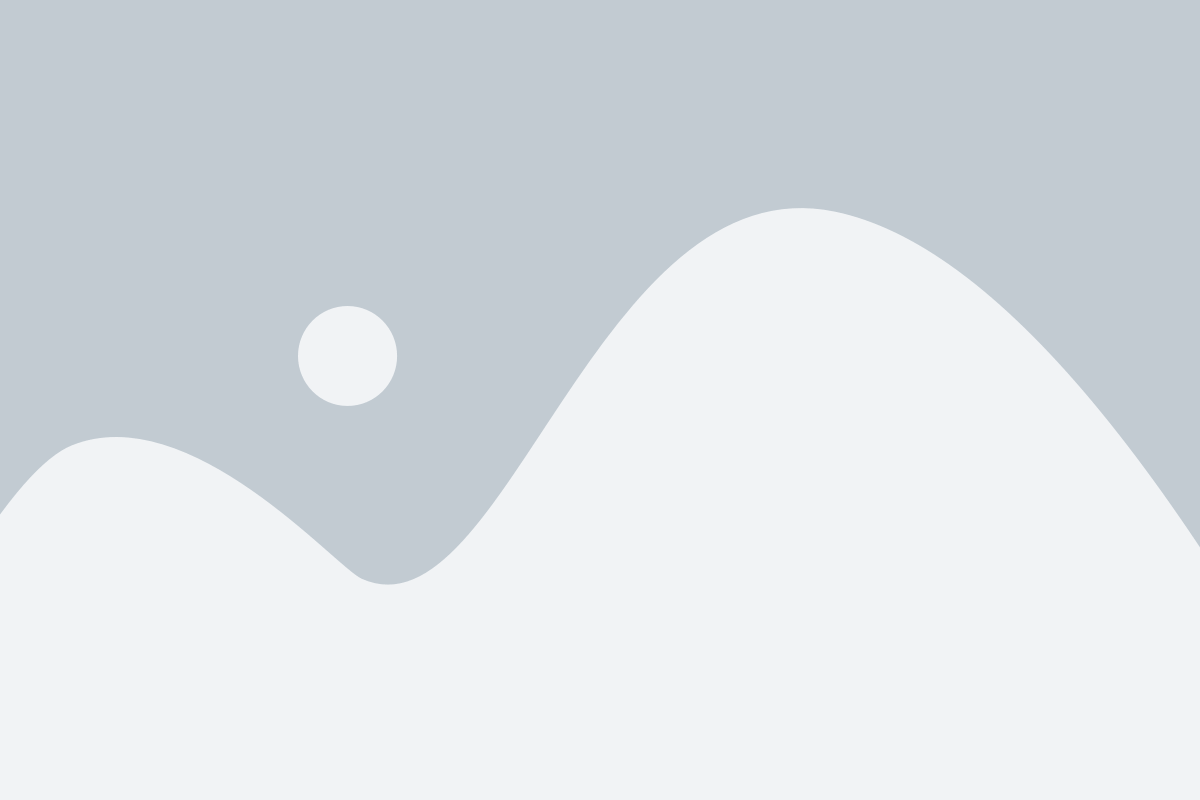
Augmented Reality
Despite its popularity in consumer applications, Augmented Reality (AR) technology is only now making inroads into the manufacturing business. Nonetheless, there is a significant untapped potential for using AR.
Manufacturers are drawn to AR because it allows workers to speed up the assembly process and improve decision-making. Workers can use AR glasses to see data projected on the physical part, such as assembly recommendations or component serial numbers, allowing for faster and easier work operations.